Током процеса гранулације машине за пелете за сточну храну, постоје појединачне пелете за храну или појединачне пелете за храну различитих боја, обично познате као "храна за цвеће". Ова ситуација је уобичајена у производњи водене хране, углавном се манифестује тако што је боја појединачних честица екструдираних из прстенасте матрице тамнија или светлија од других нормалних честица, или је боја површине појединачних честица недоследна, што утиче на квалитет изгледа целе серије хране.
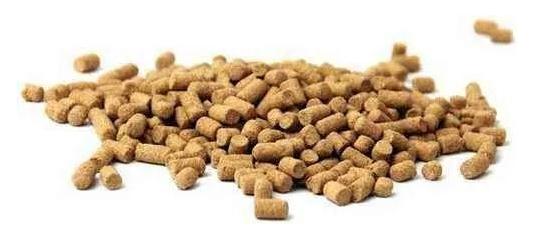
Главни разлози за ову појаву су следећи:
a)Састав сировина за животиње је превише сложен, са превише врста сировина, неуједначеним мешањем и недоследним садржајем влаге у праху пре обраде честица хране за животиње.
b)Садржај влаге у сировинама које се користе за гранулацију је недоследан. У процесу производње водене хране често је потребно додати малу количину воде у миксер како би се надокнадио губитак воде у сировинама након ултрафиног дробљења. Након мешања, шаље се у уређај за каљење. Неки произвођачи сточне хране користе сувише једноставан процес за производњу хране - ставите материјале потребне за формулу директно у миксер и додајте довољно воде, уместо да спроводе детаљан и спор процес додавања у складу са професионалним захтевима. Због тога им је тешко да обезбеде уравнотежену дистрибуцију састојака сточне хране у погледу растворљивости у води. Када користимо ове мешане састојке за третман кондиционирања, открићемо да због ефикасности регенератора садржај влаге не може брзо да се равномерно распрши. Због тога, зрелост прерађених производа за храну под дејством паре значајно варира између различитих делова, а хијерархија боја након гранулације постаје недовољно јасна.
c)У канти за гранулацију налазе се рециклирани материјали са поновљеном гранулацијом. Зрнасти материјал након гранулације може се променити у готов производ само након хлађења и просијавања. Просејани фини прах или материјал ситних честица често улази у производни процес за поновну гранулацију, обично у мешалици или чекајући силос за гранулацију. Због чињенице да је ова врста повратног материјала поново кондиционирана и гранулисана, ако се неравномерно помеша са другим помоћним материјалима или помеша са материјалима ситних честица повратне машине након кондиционирања, понекад може произвести "цветни материјал" за одређене формуле хране.
d)Глаткост унутрашњег зида отвора прстенасте матрице је недоследна. Због недоследне завршне обраде отвора за матрице, отпор и притисак екструзије које предмет доживљава током екструзије су различити, што резултира недоследним променама боје. Поред тога, неке прстенасте матрице имају неравнине на зидовима малих рупа, које могу изгребати површину честица током екструзије, што резултира различитим бојама површине за појединачне честице.
Методе побољшања из четири разлога за производњу „цветних материјала“ наведених изнад су већ врло јасне, углавном контролишу уједначеност мешања сваке компоненте у формули и уједначеност мешања додате воде; Побољшање перформанси гашења и каљења може смањити промене боје; Контролишите материјал повратне машине. За формуле које су склоне производњи "цветног материјала", покушајте да не гранулирате директно материјал повратне машине. Материјал повратне машине треба помешати са сировином и поново уситнити; Користите висококвалитетне матрице за прстенове да бисте контролисали глаткоћу отвора за матрице и ако је потребно, избрусите рупе за прстенове пре употребе.
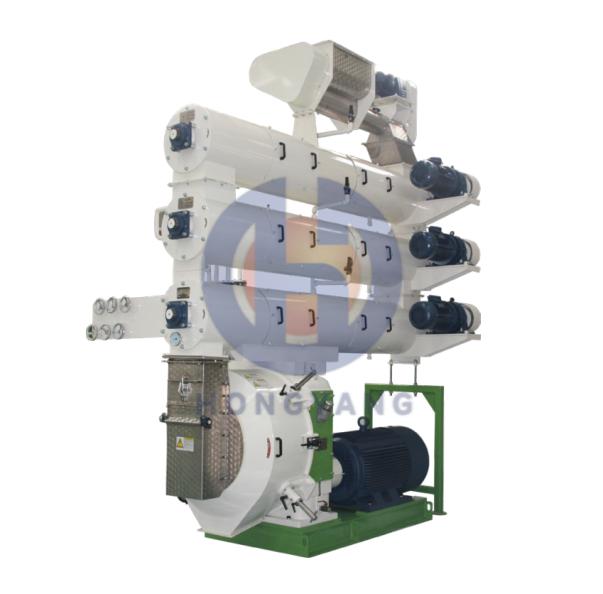
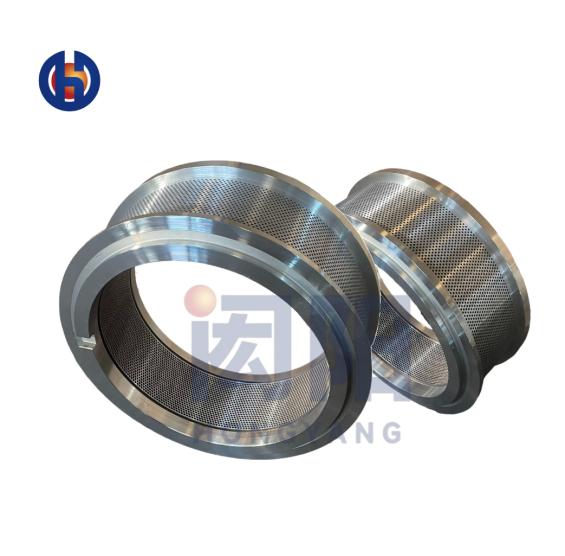
Препоручује се конфигурисање двослојног двоосног диференцијалног кондиционера и двослојног регенератора са продуженим омотачем, са временом гашења до 60-120 секунди и температуром гашења од преко 100 ℃. Гашење је уједначено и перформансе су одличне. Употреба усисног ваздуха са више тачака у великој мери повећава површину попречног пресека материјала и паре, чиме се побољшава зрелост материјала и побољшава ефекат гашења и каљења; Дигитална инструмент табла и температурни сензор могу приказати температуру клима уређаја, што корисницима олакшава контролу у било ком тренутку.
Контакт информације за техничку подршку:
Вхатсапп: +8618912316448
Е-маил:hongyangringdie@outlook.com
Време поста: 26.07.2023